How to Maintain Your CNC Tools for Longevity and Precision
Understanding the Importance of CNC Tool Maintenance
Maintaining your CNC tools is crucial for ensuring both their longevity and the precision of your machining processes. These tools are a significant investment, and proper care can help you maximize their life span and performance. Neglecting maintenance can lead to wear and tear, resulting in inaccurate machining and increased costs over time.
Regular maintenance not only extends the life of your tools but also enhances the quality of your projects. By keeping your tools in top condition, you ensure that your machining processes remain consistent and efficient, which is essential for meeting production deadlines and maintaining quality standards.

Daily Maintenance Practices
Inspect Your Tools
Begin every day with a thorough inspection of your CNC tools. Check for signs of wear, such as chips or cracks in the cutting edges. Identifying and addressing minor issues early can prevent major problems down the line.
Clean After Every Use
After using your CNC tools, clean them meticulously to remove any debris or residue. Accumulated debris can cause the tools to wear out quickly and affect their performance. Use a soft brush or cloth to clean the tools, avoiding any harsh materials that might damage them.
Weekly Maintenance Tasks
Lubrication and Calibration
Lubrication is vital for reducing friction and preventing corrosion. Make sure to lubricate moving parts regularly according to the manufacturer's instructions. Additionally, calibrate your tools weekly to ensure precision in your machining processes.
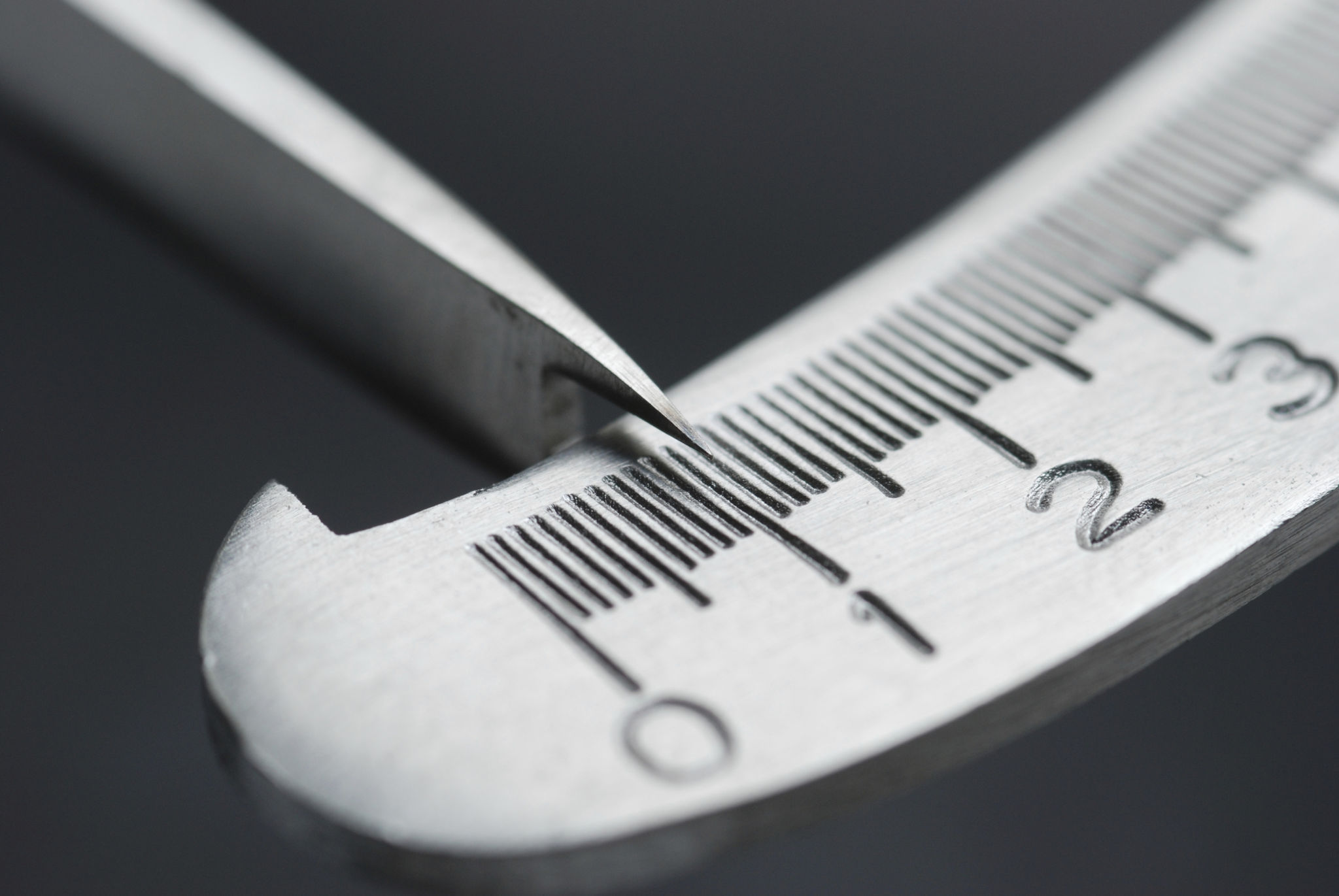
Check Tool Holders
Inspect the tool holders for signs of wear or damage. Tool holders are crucial for maintaining stability during operations. If they are worn out, they can cause vibrations that reduce precision. Replace any damaged holders promptly to maintain optimal performance.
Monthly Maintenance Routine
Sharpening and Replacement
Depending on usage, CNC tools may require sharpening to maintain their cutting efficiency. Use appropriate sharpening techniques or consider professional sharpening services if needed. Furthermore, track the life cycle of each tool and replace any that have reached the end of their useful life.
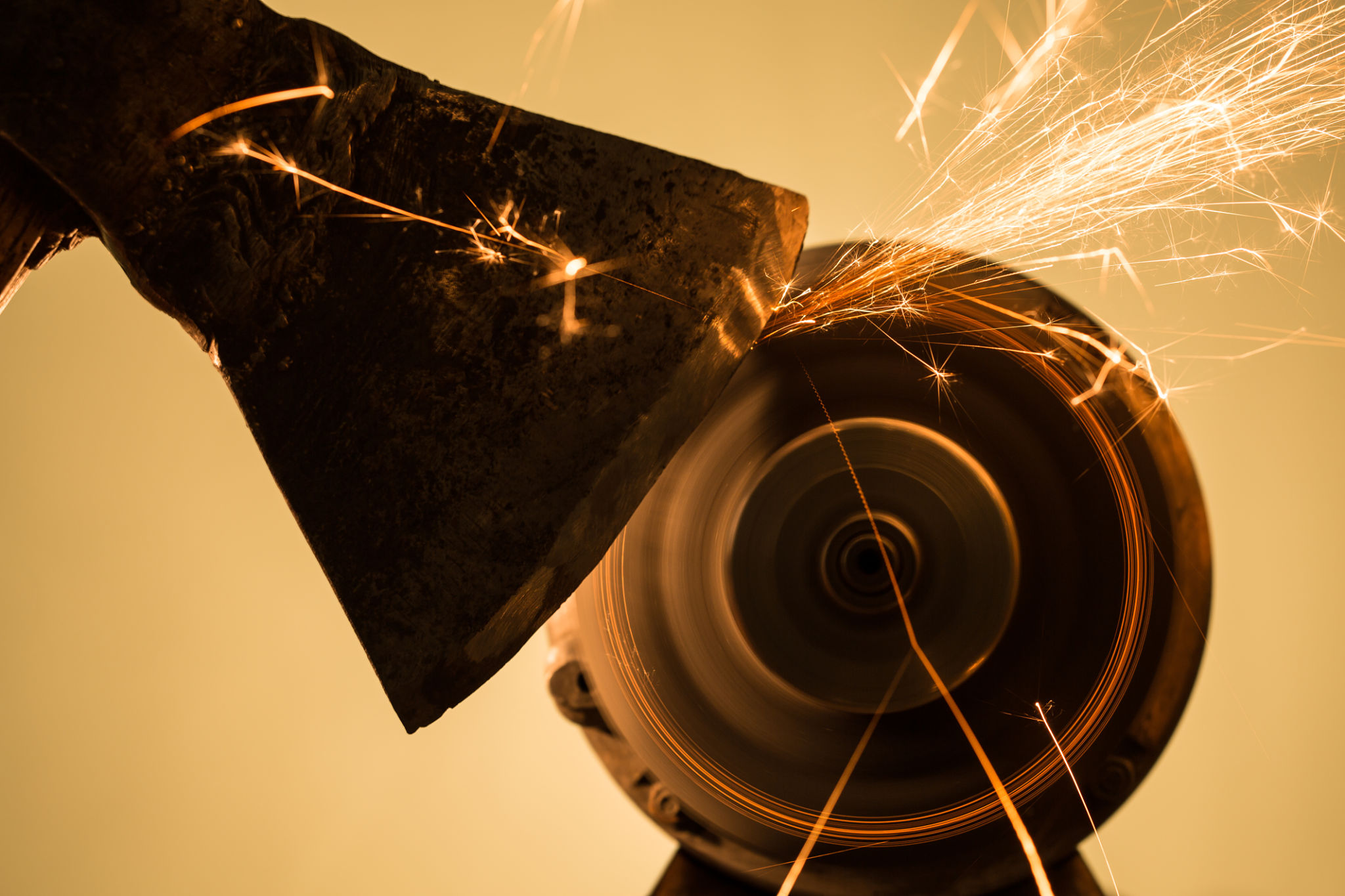
Software and Firmware Updates
CNC machines often rely on software for operation. Regularly check for updates that may improve performance or add new features. Keeping software and firmware up-to-date is essential for ensuring that your CNC machine runs smoothly and efficiently.
Training and Best Practices
Investing in training for your team can greatly enhance the maintenance of CNC tools. Educate operators on best practices and the importance of regular maintenance. Skilled operators are more likely to identify issues early and maintain high standards of tool care.
By following these maintenance strategies, you can ensure that your CNC tools remain in excellent condition, delivering precision and reliability in every project. Remember, consistent care and attention are the keys to maximizing both the lifespan and performance of your CNC equipment.